CHERRY CHINA CABINET
- Jason
- Jan 19, 2018
- 2 min read
Updated: Jan 27, 2018

This Chia cabinet was inspired by an Ethan Allen cabinet in their catalog. It is custom sized for the client. It made from solid Cherry hardwoods and Cherry veneer plywood. This is a very special piece. It took a long time to build but the final product was second to none.
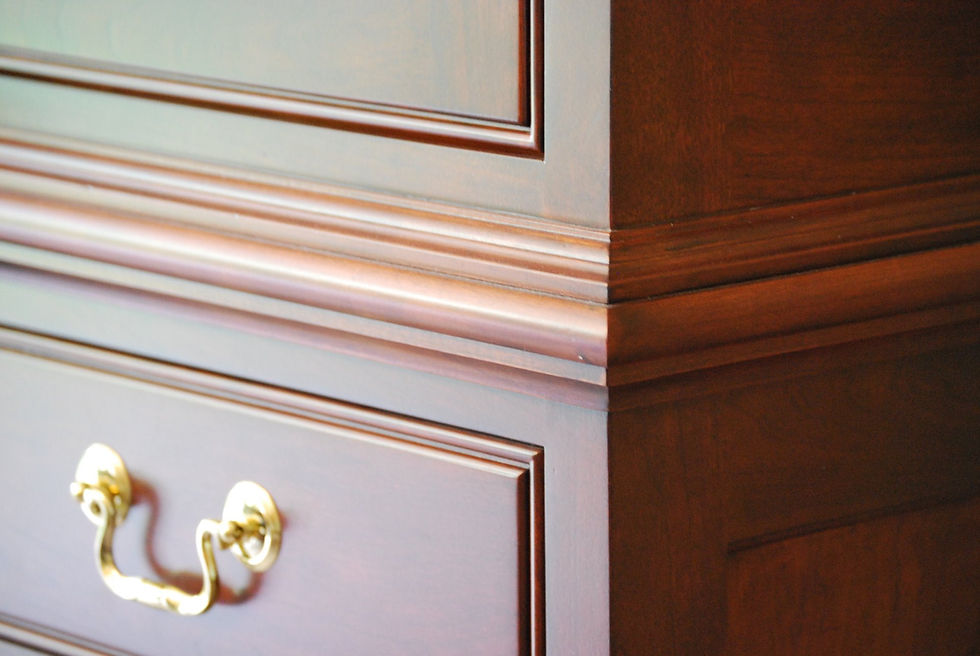
The case splits apart into a lower and upper section. Both pieces are extremely heavy, especially the top section (the glass must be removed in order to lift it) This photo shows the detail of the molding between the two sections. Also shown is the beading around the doors and drawer fronts. Not shown are the solid maple dovetail drawer boxes which added a level of quality. Below is a close up during the construction of the cabinet.
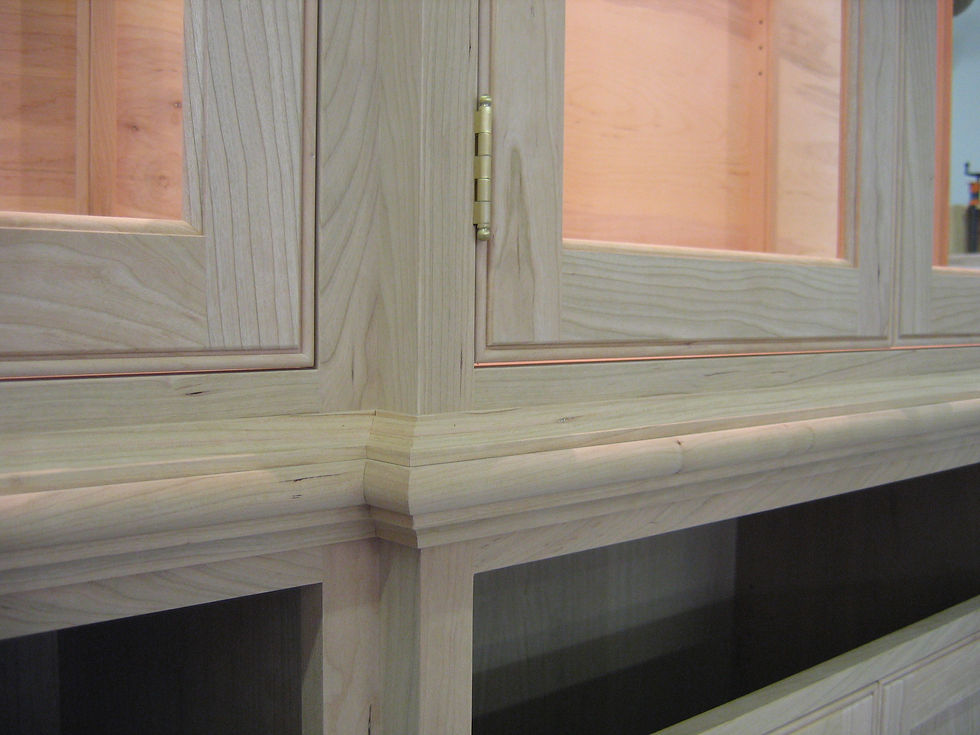

The Crown shown here was actually purchased over the web and only came in solid Poplar, however the after staining the unit with a custom wiping stain made by Sherwin Williams industrial finishes, you can't even tell it's a different species. Below is a picture during the construction.

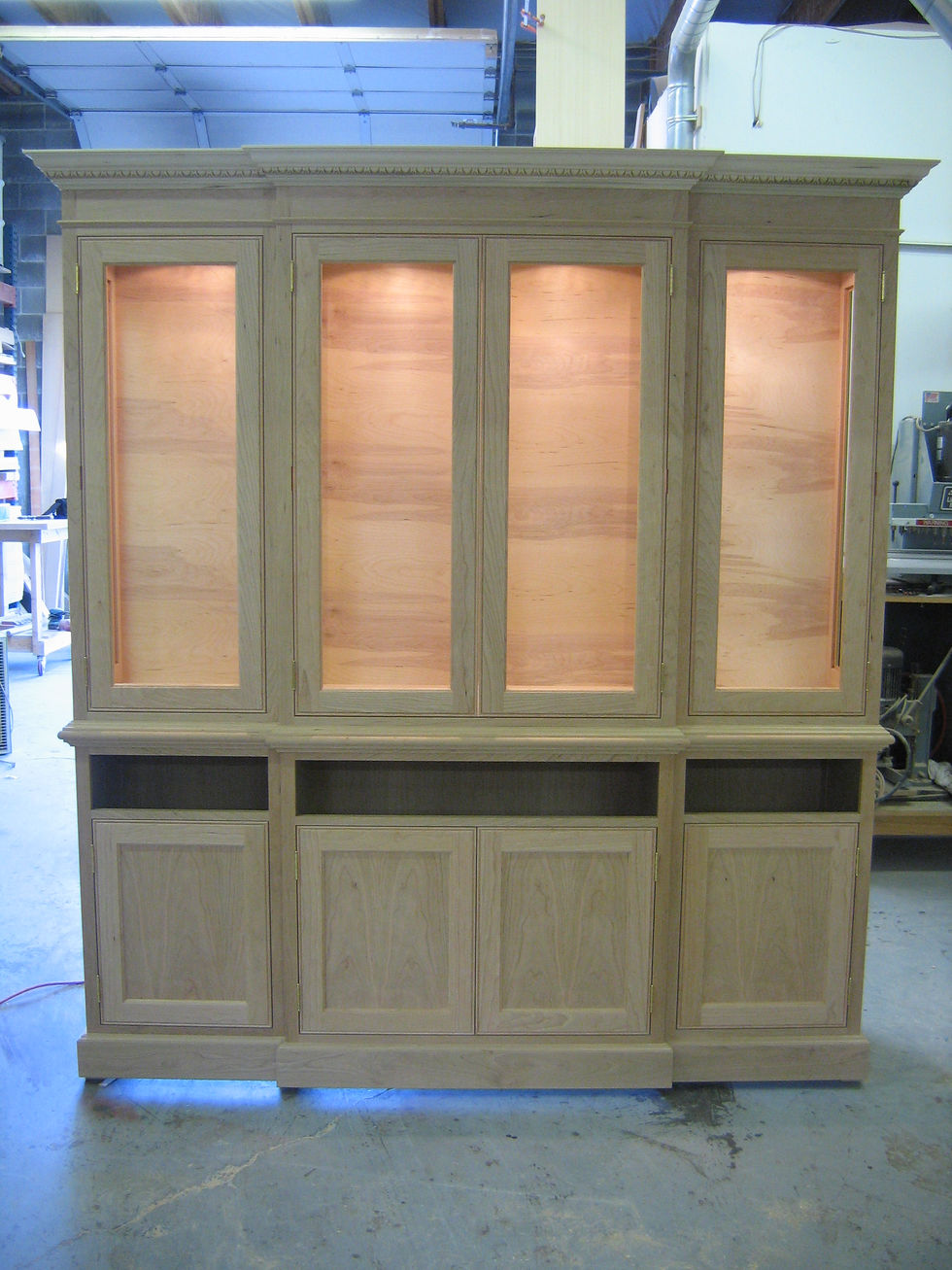
Here we are once the casework was completed. The doors are just the frames before the mullions, drawer construction at this point was still underway. The fun was just beginning

The most difficult aspect of the build was the upper glass doors. The mullions were templated and created individually. I used 1/4 MDF to make the template, making each mullion longer than needed due to each one needing to be fit to the door frame. I used a 1/8" round over bit to create the profile. The Hinges are solid brass true mortise hinges from CH Briggs Co. A small trim router and a chisel were used to mortise the hinges into the frame and doors.

Once each mullion was blanked out the fun really began. Because the inner profile of the door is a 1/4" round bead and the mullions are a 1/8" round bead the back of the mullions were coped using a 1/4" cove bit and sand paper on a 1/4" dowel. I made a small table saw sled to rough out the size of each piece. Nailing multiple guides of scrap to the sled to reproduce the same part more than once. After each piece was created I marked and created half lap joints at all intersecting pieces. The picture above is a close up of how precise each joint was made.

Final piece turned out perfect and the client was very pleased.
Comments